The Casting
The furnace used to melt the aluminum. It works by running high current through coils inside the furnace. The electromagnetic field inside the furnace causes the aluminum to vibrate so violently, the aluminum begins to melt.

The liquid aluminum drying in the plaster mold after it has been poured.

The pouring setup. The mold is placed onto a shaker table that vibrates the molten aluminum down to the bottom. A vacuum is also applied to the bottom of the mold to suck down the aluminum.
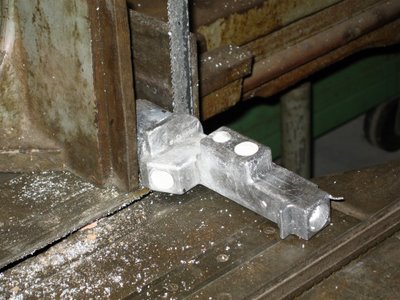
The gating system (extra metal) is being sawed off by a ban saw. The rest of the manifold has to be machined to size. Next, milling the ends flat and boring the critical holes to the right size.
