
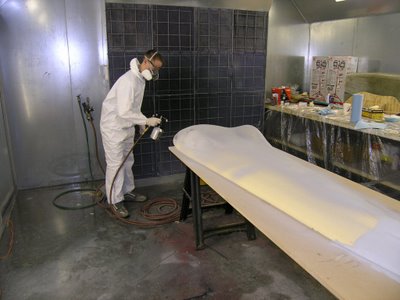

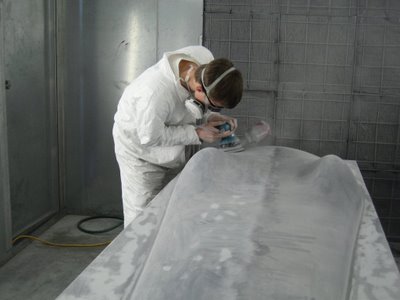

CALIFORNIA POLYTECHNIC STATE UNIVERSITY, SAN LUIS OBISPO, CA
Labels: Construction, Photo
Posted by
Unknown
at
9:04 PM
0
comments
Labels: Construction, Photo
Posted by
Unknown
at
8:52 PM
0
comments
Labels: Construction, Photo
Posted by
Unknown
at
8:44 PM
0
comments
Labels: Construction, Photo
Posted by
Unknown
at
8:34 PM
0
comments
Labels: Construction, Photo
Posted by
Unknown
at
8:30 PM
0
comments